100 W Amplifier
General Description
This is an exceptionally well designed amplifier, with a lot of power reserve, high
fidelity, low distortion, good S/N ratio, high
sensitivity, low consumption and full protection. Having all these almost ideal
characteristics this amplifier is likely to become the
basic building block of your future high fidelity system, or it can also become the
element that will upgrade your existing system.
|
 |
How it Works
The circuit works from a symmetrical ñ40 VDC power supply and draws a maximum current of
2.6 A. The input circuit of the amplifier is a differential amplifier
built around Q4 and Q5 that employ DC feedback thus preventing any DC voltage from
appearing across the speaker with the usual destructive results. Q11 acts as a current
source
and ensures that the input stage draws a constant current of 1 mA. The signal which
appears as
a voltage drop across the resistor connected in series with the collector of Q4 is used to
drive
the DARLINGTON pair Q3, Q2 which together with the constant current source of 7 mA that is
Q10, form the driver stage. This stage operates in class A and is driving the
complementary
output stage Q1, Q9. The transistor Q7 is used to balance the circuit at different
temperatures
and must be mounted on the heatsink between the out put transistors. The feedback loop
which
consists of R8, R9, C2, C3 provides AC stability to the circuit. The circuit also
incorporates a
protection stage that makes it virtually indestructible. This protection circuit is built
around Q6,
Q8. If for whatever reason the output remains connected on one supply rail and the common
the
output is also protected from high DC voltages that could burn the speakers. The supply
rails
should be protected by 2 A fuses for the 8 ohm version and 3 A for the 4 ohm.
Technical Specifications - Characteristics
Output power (f=1 KHz, d=0.5 %): 100 W in 8 ohm
Supply voltage: ................ ñ 40 V
Quiescent current: ............. 50 mA
Maximum current: ............... 2.6 A
Sensitivity: . 600 mV
Frequency response: ............ 10-35000 Hz (-1 dB)
Distortion HD: ................. 0.01 %
Intermodulation dist.: ......... 0.02 %
Signal/noise: 83 dBConstruction
PLEASE READ THIS BEFORE YOU START CONSTRUCTION
To cater for those who wish to use 4 ohm speakers with this amplifier the Kit includes the
necessary components for both versions.
The components that differ are R3,4,17 and 23. If you build the 8 ohm version then you
must also include in the circuit R28 and D7,
D8 which are not used in the 4 ohm version. As you see all the components are already
marked on the component side of the p.c.
board. The construction is made this way much simpler. Start the construction from the
pins and the jumper connections, continue
with the resistors and the capacitors and last solder in place the semiconductors. Check
each resistor before soldering it, to see if
its colours match those in the component list. Be careful with the electrolytic capacitors
because their polarity should be respected.
The polarity of those capacitors is marked on their bodies and on the component side of
the p.c. board.
NOTE: On the p.c. board next to R2, R16 are marked two other resistors which do not appear
in the circuit diagram but are included
in the components. They are of 1 ohm 2 W (brown, black, gold) and must be included in the
circuit.
Take care when you are soldering the semiconductors because if you overheat them they can
be damaged. The output transistors
should be mounted on the heatsink that is included in the kit. Take care not to short
circuit them with the heatsink and we
recommend that you use some HTC between the transistor body and the sink in order to
improve heat dissipation. Follow the
diagram for the mounting of the power transistors as it shows clearly how to insert the
insulators and the screws. Q7 should be
made to touch the heatsink and is a good idea to use a bit of HTC between its casing and
the surface of the heatsink. When you
finish the construction of your project clean the board thoroughly with a solvent to
remove all flux residues and make a careful visual
inspection to make sure there are no mistakes, components missing and short circuits
across adjacent tracks on the board. If
everything is OK you can make the following connections:
Input: 3 (signal), 5 (common)
Output: 7 (signal), 6 (common)
Supply: 1 (-40 VDC), 2 (+40 VDC) 5 (0 VDC)
Connect a milliammeter in series with the power supply, short the input of the amplifier,
turn the power ON and adjust the trimmer
P1 so that the quiescent current is about 50 mA. When you finish this adjustment remove
the shunt from the input and connect the
output of a preamplifier to it. Connect the pre amplifier to a suitable source and turn
everything ON. The signal should be heard from
the speakers clear and undistorted.
First of all let us consider a few basics in building electronic circuits on a printed
circuit board. The board is made of a thin insulating
material clad with a thin layer of conductive copper that is shaped in such a way as to
form the necessary conductors between the
various components of the circuit. The use of a properly designed printed circuit board is
very desirable as it speeds construction up
considerably and reduces the possibility of making errors. Smart Kit boards also come
pre-drilled and with the outline of the
components and their identification printed on the component side to make construction
easier. To protect the board during storage
from oxidation and assure it gets to you in perfect condition the copper is tinned during
manufacturing and covered with a special
varnish that protects it from getting oxidised and makes soldering easier. Soldering the
components to the board is the only way to
build your circuit and from the way you do it depends greatly your success or failure.
This work is not very difficult and if you stick to
a few rules you should have no problems. The soldering iron that you use must be light and
its power should not exceed the 25
Watts. The tip should be fine and must be kept clean at all times. For this purpose come
very handy specially made sponges that
are kept wet and from time to time you can wipe the hot tip on them to remove all the
residues that tend to accumulate on it. DO
NOT file or sandpaper a dirty or worn out tip. If the tip cannot be cleaned, replace it.
There are many different types of solder in the
market and you should choose a good quality one that contains the necessary flux in its
core, to assure a perfect joint every time.
DO NOT use soldering flux apart from that which is already included in your solder. Too
much flux can cause many problems and is
one of the main causes of circuit malfunction. If nevertheless you have to use extra flux,
as it is the case when you have to tin
copper wires, clean it very thoroughly after you finish your work. In order to solder a
component correctly you should do the following:
- Clean the component leads with a small piece of emery paper.
- Bend them at the correct distance from the component body and insert the component in
its place on the board.
- You may find sometimes a component with heavier gauge leads than usual, that are too
thick to enter in the holes of the p.c.
board. In this case use a mini drill to enlarge the holes slightly. Do not make the holes
too large as this is going to make soldering
difficult afterwards.
- Take the hot iron and place its tip on the component lead while holding the end of the
solder wire at the point where the lead
emerges from the board. The iron tip must touch the lead slightly above the p.c. board. -
When the solder starts to melt and flow,
wait till it covers evenly the area around the hole and the flux boils and gets out from
underneath the solder. The whole operation
should not take more than 5 seconds. Remove the iron and leave the solder to cool
naturally without blowing on it or moving the
component. If everything was done properly the surface of the joint must have a bright
metallic finish and its edges should be
smoothly ended on the component lead and the board track. If the solder looks dull,
cracked, or has the shape of a blob then you
have made a dry joint and you should remove the solder (with a pump, or a solder wick) and
redo it. - Take care not to overheat the
tracks as it is very easy to lift them from the board and break them.
- When you are soldering a sensitive component it is good practice to hold the lead from
the component side of the board with a pair
of long-nose pliers to divert any heat that could possibly damage the component.
- Make sure that you do not use more solder than it is necessary as you are running the
risk of short-circuiting adjacent tracks on
the board, especially if they are very close together.
- When you finish your work cut off the excess of the component leads and clean the board
thoroughly with a suitable solvent to
remove all flux residues that still remain on it.

If it does not work
Check your work for possible dry joints, bridges across adjacent tracks or soldering
flux residues that usually cause problems.
Check again all the external connections to and from the circuit to see if there is a
mistake there.
- See that there are no components missing or inserted in the wrong places.
- Make sure that all the polarised components have been soldered the right way round. -
Make sure the supply has the correct
voltage and is connected the right way round to your circuit.
- Check your project for faulty or damaged components.
If everything checks and your project still fails to work, please contact your retailer
and the Smart Kit Service will repair it for you.


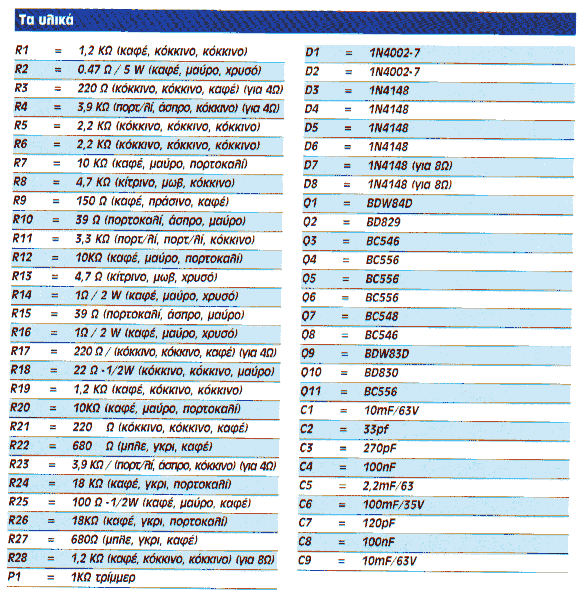
L1 : 10 coil with wire 0,5mm turned on a restistor of 1W
|