Video Digitizer
This circuit was designed by W. A. Steer in the U.K. His site
can be accessed at: http://www.ucl.ac.uk/~ucapwas/
The design is based around the ubiquitous BT218 video A/D
converter and interfaces to a PC via an EPP compliant parallel
port. The text from here on is Andrew's:

A "video-digitiser" captures television pictures
from a TV set, camera, or video recorder, etc., and forwards them
to a computer for display, storage, or general manipulation. This
document describes a home-built digitiser which interfaces to an
EPP (or bi-directional) parallel port on IBM PCs.
Video digitiser - technical details
The present design digitises pictures to very high quality in
monochrome (8-bit black & white). Although designed for the
European standard 625-line / 50Hz TV system, it should work with
the American 525-line / 60Hz standard with minimal modification.
Before embarking on the project, please be sure to realise that
this design will not capture movies. At best, it
can manage a couple of frames per second. Note also that as
described, the circuit collects its picture from a succession of
frames. Consequently the image must remain fairly still for the
half-second or so taken to capture it. A competent constructor
could purchase a larger and more expensive memory chip and modify
(simplify) the circuit to overcome the latter limitation if
desired.
Introduction and Circuit overview
Television equipment uses a simple composite video signal
which carries all the picture information. Pictures are conveyed
as a continuous sequence of frames, each taking 1/25 second.
Within each frame are 625 horizontal scan lines, transmitted in
turn starting at the top. [To reduce flicker, each frame is
actually transmitted as two consecutive fields, the first
containing odd-numbered lines, and the second filling in the even
numbered, a technique known as interlacing. This cunning trick ups
the refresh rate to 50Hz, without increasing the signal
bandwidth.]
All video recorders and many TV sets will have a composite
video output, usually using a BNC or phono socket. The 21-pin
SCART socket found on most domestic AV equipment these days also
has a composite video out pin.
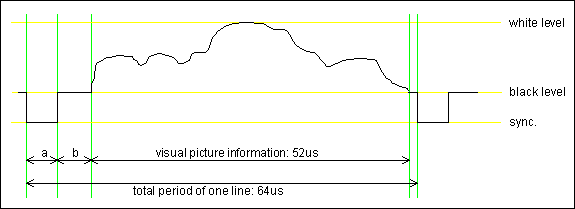
Structure of one video line
In the signal increasing voltage corresponds to increasing
brightness. Picture lines are separated by a brief "sync
pulse", during which the voltage goes below that of total
blackness. Usually the "sync level" is 0V, black level
0.3V, and peak white 1.0V.
In the diagram, region a is the sync, b is the
"back porch" (at black level). These are followed by the
picture information, finishing with a brief "front
porch" (also at black level) before the next line sync.
Frames are separated by longer duration sync pulses.
Exact timings are given in the table below.
frame field line- back picture front line
lines rate rate sync porch data porch total
European 625 25Hz 50Hz 4.7us 5.8us 52.0us 1.5us 64.0us
system
US system 525 30Hz 60Hz 4.7us 4.7us 52.66us 1.5us 63.56us
Note that the "625 lines" means that the line period
is 1/625 that of the frame rate. Because the equivalent of several
lines is spent in frame syncs, and a further 25 lines at the top
of the screen are used to carry teletext information, there are
only normally 576 lines of visual data. Some similar decrease will
apply to the 525/60 US system.
The broadcast bandwidth is limited to 5-6MHz, giving a maximum
horizontal resolution equivalent to about 600 pixels.
Given the above information, in order to capture all the
information in a picture it is clearly necessary to digitise the
composite video signal at a rate of around 10 million samples per
second. Since your average parallel port cannot possibly take data
at that rate, some kind of hardware buffer is required - taking
data on board at high speed, and releasing it slowly to the
computer's port. Modern high-speed First-In First Out (FIFO)
memory devices make incredibly simple and convenient buffers.
See block diagram for overall schematic.
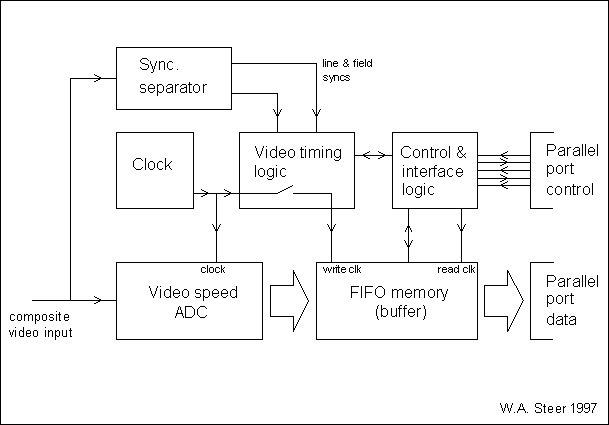
I chose the Bt218KP-20 analog to digital converter because of
its high specification and very reasonable price. I could have
chosen a 256kb "frame buffer" FIFO, which would permit
capture of a whole frame in one go, but for reasons of cost (and
because I had other ideas I wanted to experiment with which
required only a small buffer), I have used only a 2048byte FIFO,
the Am7203A. A natural consequence of using a small buffer is that
one picture has to be captured in several goes, spanning about a
dozen frames. In the present design "blocks" of 4 scan
lines of 512 pixels are captured at a time, then downloaded to the
PC. Fast action scenes will inevitably tend to get broken up.
In addition to the ADC and FIFO, a handful of logic gates are
required to handle the control and handshaking for the EPP
computer interface. Another small section of logic circuitry
ensures that we only bother digitising the part of each video
signal scan-line which contains useful picture information.
Finally a larger module consisting of a binary "scan
line" counter and a magnitude comparator is used to govern
the collection of "blocks" of 4 scan-lines at a time
(and could be omitted if you designed a version with a full-frame
FIFO buffer).
Computer parallel ports
At this point, a brief diversion on parallel port types is
warranted.
All parallel ports have eight "data lines", four
output "control" lines, and five input
"status" lines. In the original PC, the standard
parallel port data lines were essentially output-only (ok... there
were hacks!). By a trivial design modification IBM introduced
"bi-directional" data lines on their PS/2 model,
where the output-drivers could be software disabled and data read
in using the so-called read-back register. Unfortunately these
didn't generally catch on.
Up to this point all inputs/outputs used TTL signal levels, and
timing and cable specifications were very lax.
Then in the mid nineties, a new range of "enhanced"
parallel ports appeared. Basically they tightened up all the
electrical specifications, made the data lines bi-directional, and
added hardware flow control and data buffering, so that the
throughput could be increased dramatically, up to 2MB/sec [though
I find 500kB/sec is about the upper limit on my PC, but then it is
an old machine with slow bus.]
Enhanced parallel ports come in two flavours of transmission
protocol: EPP (enhanced parallel port) which essentially
just automates and accelerates the standard handshaking, with
extensions for input ability, and ECP (enhanced capability
port) which goes a whole stage further with DMA data in/out and
scope for hanging multiple devices off one port - making it
practically a poor-mans SCSI!
As you might have guessed, implementing ECP in a hardware
project would require little short of a microprocessor (or at
least LSI chips). For home constructors the EPP-type port provides
pretty much all you could want, and is by far the easiest to use.
Most modern PC I/O cards which claim to be "enhanced"
or "1284" (see below) will support both protocols,
though the settings may be determined by jumpers.
This digitiser circuit requires an EPP type enhanced port.
Parallel ports and especially the enhanced ports are defined in
standard IEEE 1284. An excellant abbreviated version of IEEE 1284
is available online at the FAPO web site.
Circuit schematics and major parts list

Sheet 1 |

Sheet 2 |
[Note: Vcc = +5v throughout ]
IC1 EL4581CN Video sync-separator
IC2 74HC14 Hex schmitt inverting buffer
IC3 74HC4040BE 12-bit binary ripple counter
IC4 74HC688 8-bit magnitude comparator
IC5 (no longer required - task now done by IC4)
IC6 74HC4040 12-bit binary ripple counter
IC7 74HC00 Quad 2-input NAND gate
IC8 74HC74 Dual D-latch
IC9 74HC02 Quad 2-input NOR gate
IC10 74HC4040 12-bit binary ripple counter
IC11 40MHz crystal oscillator module
IC12 Bt218KP-20 Video-speed ADC
IC13 Am7203A-35RC High speed 2048byte 9-bit FIFO buffer
IC14 74HC14 Hex schmitt inverting buffer
The Bt218KP-20 Video-speed ADC is manufactured by Brooktree, a
division of Rockwell Semiconductor.
The Am7203A-35RC High-speed FIFO buffer is manufactured by
Advanced Micro Devices (AMD), but pin-for-pin equivalents from
other suppliers are available.
The EL4581CN video sync separator is made by Elantec, and similar
parts are made by National Semiconductor.
Data sheets for the 74HC logic family are available in PDF format
from the Texas instruments website.
Circuit description
[Sheet 1]
A 40MHz crystal oscillator module keeps the circuit ticking and
directly drives the clock input of a 12-bit binary counter which
acts as a clock frequency divider. The 10MHz tap acts as the clock
for the ADC, and is conditionally gated (see below) before feeding
the FIFO's write-clock input. In an early stage of the design
development it was found necessary to "lock" the phase
of this 10MHz clock to the incoming video line-sync to prevent the
picture wandering sideways by one pixel, and was achieved by
resetting the binary counter during line-syncs. If just a 10MHz
crystal oscillator were used instead then this phase-locking would
not be possible.
Video Timing
[Sheet 2]
A standard sync-separator IC is used to obtain frame and line
syncs. The "porch" output, active during the back porch
period, is fed to the ADC zero/clamp input and facilitates
black-level clamping and periodic zeroing of the ADC's internal
comparators [the data sheet requires this be done periodically].
Within each video scan-line we want to ensure that only the
useful picture data is stored, and not waste precious space in the
FIFO with line syncs and porches. Comparing the video signal with
the output of the "master clock divider" binary counter,
which is reset during line-syncs, reveals that Q9 goes high at
about the times we want data-storage to both commence and cease,
with Q12 being low at the start and high at the finish.
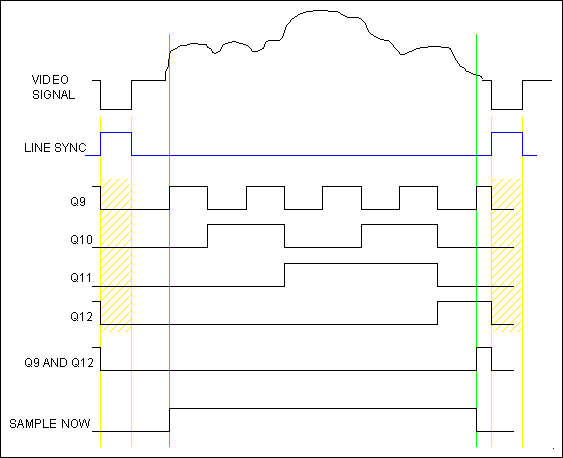
Line timing for data-collection
In the diagram, the trace marked "SAMPLE NOW" shows
the signal we would like to derive in order to control the storage
of data.
[Sheet 2, inset]
At present, a clean "high to sample" signal is obtained
quite elegantly using a 'D'-latch clocked by Q9 and data input
from NOT Q12. [ In reality, the "correct block" signal
(see below) is also brought into the logic equation at the point
where Q12 inverted.]
Given that the method of switching the FIFO write clock using
the NAND gate is not inherently synchronous, care is required to
ensure we change the state of the control input only while the
FIFO clock is HIGH (inactive) that is, when the main clock is LOW.
Failure to comply will result in write pulses of sub-standard
duration, and possibly jitter on the picture. Since output Q9 of
the binary counter changes following the FALLING edge of Q2, the
main clock, all should be well. BUT we have to be careful about
propagation delays, 8ns typ. for 74HC logic gates, 21ns for the
74HC74 dual D-latch, given that the clock changes state every
50ns! Possibly the biggest problem is that the 74HC4040 is a
ripple counter - I ought to (but don't) know how much delay there
is between Q2 changing state and Q9 following it!
A further binary counter, IC3, with its clock input connected
to the line-sync, and reset to the field-sync, keeps track of the
number of the scan line currently being broadcast. Discounting the
lower two bits effectively divides the count by four, yielding the
current "block" of 4 lines. Using an 8-bit magnitude
comparator, IC4, this is compared to the number of the block
"requested" by the software (via counter IC6). In this
latest design, the top bit of the comparator compares the field
(odd/even) and permits pictures to be captured using the full
vertical resolutions. The magnitude comparator gives an high
output at J "correct block" when the numbers match.
The real "high to sample" signal is generated by
gating the control of our hypothetical "SAMPLE NOW"
signal using the "correct block" signal, and completes
the organisation of data collection.
Lastly, it is a requirement of the FIFO that both its -Read and
-Write clocks must be de-asserted (ie HIGH) during a FIFO reset to
guarantee proper operation. This condition has been taken care of
in the logic.
[Sheet 1]
On the output-side of the FIFO, logic tailors the EPP control
signals to meet the requirements of the FIFO read clock.
Essentially, when -Write is HIGH and -DataStb is LOW, the -ReadClk
input of the FIFO is asserted, which causes it to assert data on
its outputs and then increment its internal read-pointer. At all
other times the FIFO outputs are high-impedance. A slightly
retarded (and inverted) copy of the FIFO -ReadClk provides the EPP
-Wait handshake signal. The FIFO -Empty flag is connected to a
user input on the parallel port so software can test when data
becomes available. Software asserts the EPP -Write signal (making
it LOW) to reset the FIFO and increment the "requested
block" counter, and the EPP -Reset connection is used to
reset the "requested block" counter to zero before
commencing a frame-grab. [I may soon replace the "requested
block counter" by an 8-bit latch fed from the parallel port
so that the computer can be in full control of which lines are
collected.]
Miscellaneous details:
With UK PAL standard, a colour sub-carrier at 4.43MHz is added to
the broadcast composite video signal, which on a black and white
set manifests itself as fine cross-hatching on regions of the
picture which had saturated colours. This fine pattern gets
aliassed when sampled, and tends to put a "mesh effect"
over the picture. A simple low-pass filter could be used to
eradicate it, but a strong enough filter of that type blurs the
picture unacceptably. I implemented a 4.43MHz L-C notch filter. I
believe the NTSC sub-carrier lies at about 3.5MHz, so readers from
the States (or Japan) will need a slightly larger capacitance!
[See input to ADC, on sheet 1]
At one stage I found I had mild vertical streaking on my
digitised picture, so it looked a bit like a dodgey photocopy. The
problem was fast digital signals getting coupled to the video
signal, and the solution was to keep the analog parts away from
the digital as far as is reasonably possible, keep leads short,
and use a good smothering of decoupling capacitors across the
supply rails, particularly next to the clock-divider binary
counter. With these precautions my prototype, built on BimBoards,
functions perfectly acceptably so requirements don't seem to be
too stringent! See the ADC data sheet for more hints on board
layout.
All the (DC-level voltage and drive current) interfacing
between ICs (ADC, FIFO, control logic...) appear to be within
spec., but strictly the FIFO output does not have enough drive
current to meet the IEEE 1284 specifications for EPP compatible
devices (although it works fine on my particular card). Ideally a
buffer IC would be used to interface the EPP data "bus"
(and this would also serve to protect the FIFO in the event of a
fault, static discharge etc. on the plug).
Software control
Before digitising a scene, the computer should set the EPP -Reset
line low momentarily to reset the "block counter", then
go into a block-collecting loop which repeats for 70 or so blocks:
- briefly lower the -Write line to clear the FIFO and
increment the circuit's block counter
- wait for EPP user input (S3+) to go HIGH, signifying that
the FIFO has some data
- loop reading 2048bytes from the FIFO using the parallel port
EPP data register. (Non-EPP bi-dir port users will have to do
the handshaking manually.)
- other processing [eg. copy the data to a bitmap]
See my other pages for details of the software interface
presented by parallel ports.
Ideally, for fastest performance (particularly if trying to
"interlace" blocks - see below) it'd be better to pulse
low the -Write line immediately after reading the data, and before
doing additional processing so the circuit can be acquiring the
next block in the mean time.
If after downloading one block, we wait for the next field and
collect the next block then one picture will take 576 lines/4
lines = 144 fields (72 frames), or 2.88 seconds. Hence significant
movement in the scene will cause the digitised image to break up
somewhat. But we can improve on this: data comes in at 10MHz, and
is read out by the computer at approaching 2MHz (on an EPP port) -
so the computer will be busy for little over 5 blocks for every
one block sampled. From then on, it'd be idly waiting for the next
frame to be broadcast. A better idea is to get the circuitry to
collect (say) blocks 0,8,16,24,32,... from the first frame,
1,9,17,25,33,... from the next, and 2,10,18,26,34,... etc from the
following frame and so on. That way it'll only take a fifth of a
second to capture a whole picture (in theory) - a vast
improvement. The maximum degree of such interlacing you can manage
all depends on the speed of your PC.
With the present hardware it is possible to implement the above
scheme by sending multiple "next block" requests to the
hardware to get it to retrieve block 8 after block 1, etc., but
for a neater and more flexible approach I'd like to try using an
8-bit latch to store the number of the "requested
block".
If you need faster throughput and don't mind sacrificing
vertical resolution, you could just collect half the vertical
lines, and very simply modify the circuit to not care which field
it samples.
TIMING DIAGRAMS
component requirements
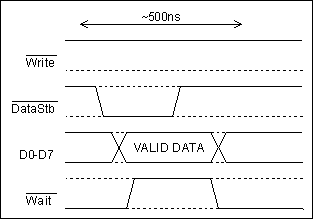
EPP data read cycle (source: FarPoint Communications web page)
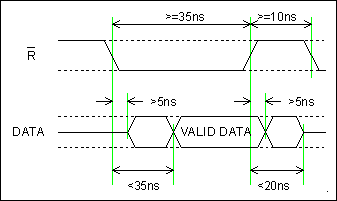
FIFO [Am7203A-35RC] read cycle (source: AMD FIFO data book)
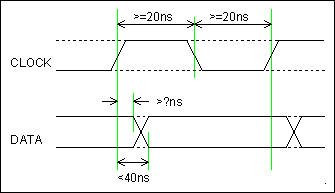
Video ADC [Bt218KP-20] timing (source: Brooktree advance
information (data sheet) 8/9/91)
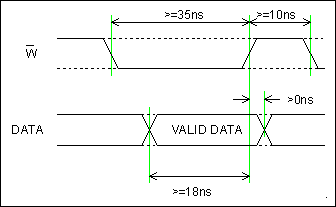
FIFO [Am7203A-35RC] write cycle (source: AMD FIFO data book)
Future development
To increase the circuit's simplicity and elegance, and to make it
more robust (in all senses), I plan to look into the following
modifications soon:
- Replace the 74HC4024 "requested line" counter with
an 8-bit register (data latch), so the computer can more
easily specify which block it wants.
- Buffer the data lines to the EPP port. Strictly, the FIFO
doesn't have enough output drive to meet EPP the spec.,
although it seems to work ok with my card.
- Modify the Vref arrangement on the ADC slightly to implement
a brightness preset control (caution, this adaptation is prone
to increase noise in the sampled waveform).
- Write software to decode the sampled PAL colour
information (when the carrier hasn't been suppressed) and
colorise the picture.
January 1999: have done this with great success! Refer
to my video
digitiser root page for the latest on this project, and
progress on a new improved, and simplified, digitiser circuit.
Disclaimer
How to save and view
schematics
|